6 Trimble Transportation Bridge the Divide Bridge 1: Operations By crossing this bridge, transportation companies will bring together parallel functions in maintenance and operations to maximize asset availability and utilization. Trimble Fleet Maintenance and TMS systems have pre-built integrations that give visibility to load planners for matching the right equipment and accessories with loads and drivers. Operations also can identify assets in the TMS that are unavailable for dispatch and take an active role in routing vehicles to shops for PM intervals, equipment inspections and repairs that are coming due. Canada-based Bison Transport in Winnipeg, MB, has proactive notifications sent automatically from its Trimble Fleet Maintenance system to operations. With this visibility, personnel in operations play an active role in scheduling and routing equipment to the company’s five internal shops. The custom dashboards help the departments coordinate shop appointments and schedules, says Trevor Johnston, Bison’s maintenance analyst. “Our daily dashboard audits allow us to stay on top of any scheduling conflicts,” he says. Estes Express Lines has a live dashboard in the operations room that gives real-time visibility of breakdown status. Out-of-service trucks are displayed with the time remaining for dispatch availability, says Mike Palmer, vice president of Fleet Services. “Our goal is to be up and running in two hours,” he says. The custom application was developed in house by Estes, a full-service freight transportation provider with a network of more than 230 terminals. The software combines equipment status and locations from its fleet maintenance and mobility systems from Trimble. Bison’s maintenance and operations have visibility of key metrics for more than 1,500 power units and 5,000 trailers in real-time dashboards.
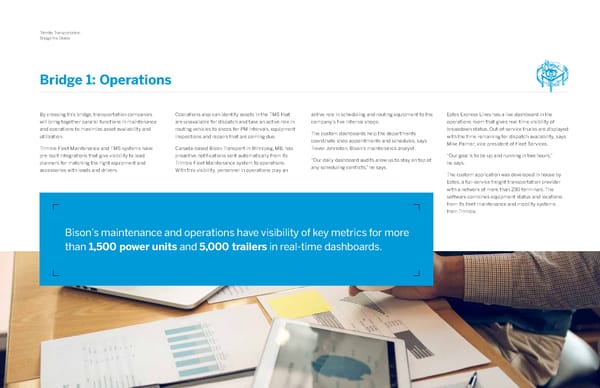